Test Work Proves Up Processing Pathway For Australian Vanadium
Special Report: With vanadium extraction of up to 95.5 per cent in the bag, Australian Vanadium is now carrying out pyrometallurgical testwork for its definitive feasibility study (DFS).
Laboratory testwork carried out to simulate the industry standard Grate Kiln process had resulted in improved vanadium extraction averaging about 92 per cent compared to traditional rotary kiln extraction of between 85 to 88 per cent.
Australian Vanadium (ASX:AVL) said this was achieved by pelletising concentrate produced by preliminary beneficiation from its namesake project near Meekatharra, Western Australia.
This concentrate was then subject to oxidative salt roasting to simulate a commercial straight Grate Kiln, which has a track record in the iron ore, titanium and steel industries.
The company said that pellet processing using this process had the advantages of higher reaction progress, greatly reduced kiln build up, significant reduction in dust loss and ease of process control and heat recovery.
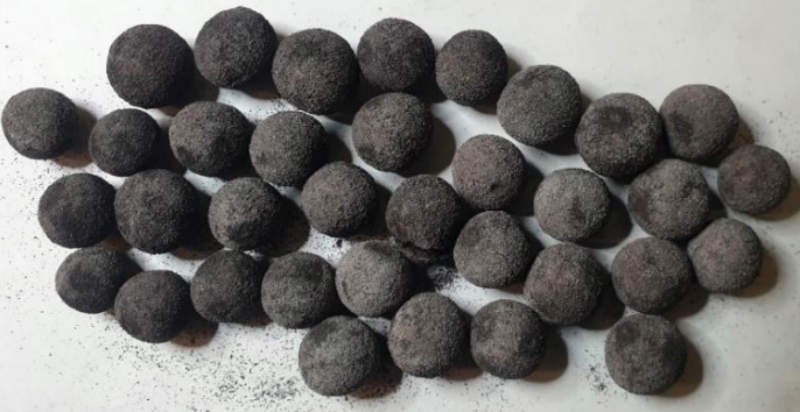
And the proof is in the pudding, with vanadium extraction reaching a top of 95.5 per cent under optimised temperatures, bed depths and retention times.
This compares with the vanadium roast extraction of 87.9 per cent achieved during the company’s pre-feasibility study.
“Our vanadium ore is very well suited to the traditional salt-roast methods, but we see opportunity in our testwork for processing improvements that could lead us to a world-leading position when in production,” managing director Vincent Algar said.
“Improved vanadium recoveries, coupled with the potential to reduce gas consumption and related operating cost reductions, further reinforces the project’s position as a desirable investment.
“Utilising the Grate Kiln technology is an innovation that our highly technical team has pursued as a result of the diligent testwork they are undertaking.
“Improving the economics of our project is the company’s key driver as we take each step forward.”
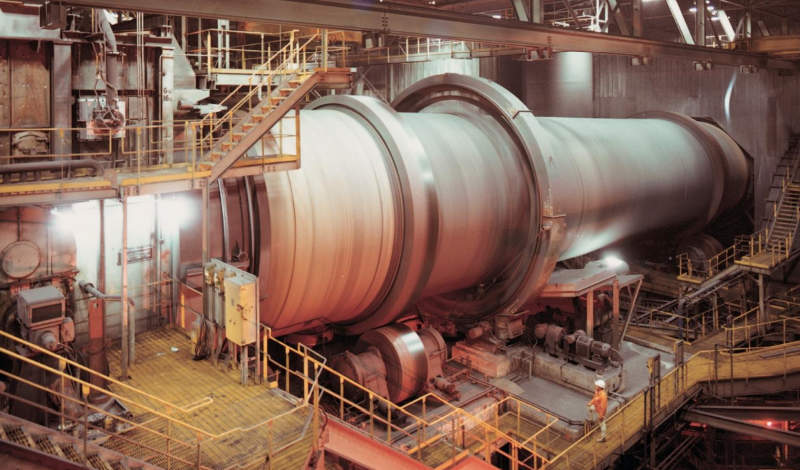
A 2-tonne sample of vanadium concentrate produced by the crushing, milling and beneficiation pilot in Perth is in transit to Metso’s Pyro Technology laboratory located in Danville, Pennsylvania.
Testing by Metso is aimed at optimising process economics and confirm design parameters for the project’s Grate Kiln flowsheet.
Completion of this test work is expected to deliver a high degree of certainty in forecasting full scale Grate Kiln performance and in the estimation of associated capital and operating costs for the DFS.
This story was developed in collaboration with Australian Vanadium, a Stockhead advertiser at the time of publishing.
This story does not constitute financial product advice. You should consider obtaining independent advice before making any financial decisions.
www.stockhead.com.au/